机床铸件底面气孔:全新解决方案
本文将详细阐述机床铸件底面气孔的全新解决方案。介绍了机床铸件底面气孔的问题和影响;然后,从六个方面分别阐述了解决方案:材料选择、设计优化、工艺改进、设备升级、检测手段和质量控制;总结归纳了全文的内容。
一、问题和影响
机床铸件底面气孔是制造过程中常见的问题,会对机床的性能和使用寿命产生负面影响。气孔会降低机床的强度和刚性,导致机床变形和振动加剧,进而影响加工精度和稳定性。气孔还可能引起润滑不良、渗漏和噪音等问题,严重影响机床的正常运行。
二、材料选择
材料选择是解决机床铸件底面气孔问题的关键。应选择具有良好流动性和抗气孔性能的铸造材料,并严格控制材料的成分和熔炼工艺。采用先进的材料检测手段,确保材料质量符合要求。
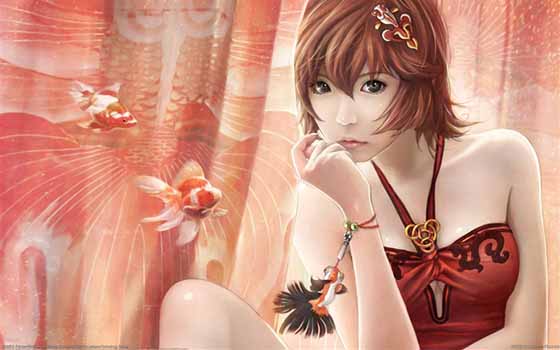
三、设计优化
在机床铸件的设计过程中,应注重减少气孔产生的可能性。通过合理的结构设计和优化,减少气孔的滞留区域和难以排除的死角,提高铸件的整体密封性和排气性能。还应考虑铸件的壁厚、孔径和孔距等参数的合理选择,以减少气孔产生的概率。
四、工艺改进
工艺改进是解决机床铸件底面气孔问题的重要手段。应优化铸造工艺参数,如浇注温度、浇注速度、浇注方式等,以提高铸件的充型性和减少气孔的产生。采用适当的浇注系统和浇注工艺,确保熔融金属在铸件中充分流动和排气,减少气孔的形成。
五、设备升级
设备升级是改善机床铸件底面气孔问题的有效途径。应引进先进的铸造设备和技术,提高铸件的制造精度和一致性。采用自动化控制系统和智能化设备,实现对铸造过程的精确控制和监测,减少人为因素对气孔产生的影响。
六、检测手段和质量控制
为了及时发现和控制机床铸件底面气孔的问题,应建立完善的检测手段和质量控制体系。采用先进的无损检测技术,如X射线、超声波等,对铸件进行全面检测和评估。建立严格的质量控制标准和流程,确保铸件的质量稳定和可靠性。
总结归纳
机床铸件底面气孔是制造过程中常见的问题,会对机床的性能和使用寿命产生负面影响。为了解决这一问题,我们可以从材料选择、设计优化、工艺改进、设备升级、检测手段和质量控制等六个方面入手。通过合理的措施和方法,可以有效减少机床铸件底面气孔的产生,提高机床的质量和可靠性。全新的解决方案为机床铸件底面气孔问题的解决提供了可行的途径。